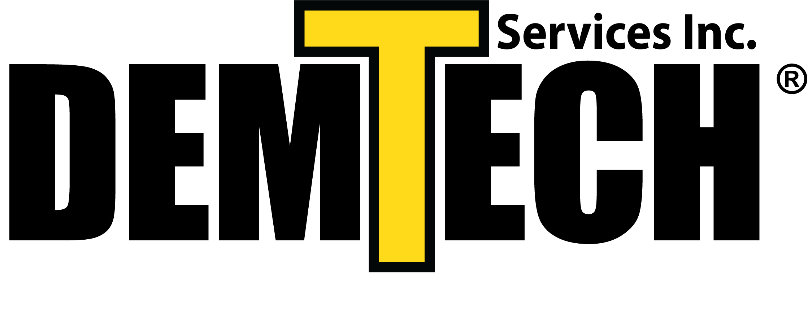
Pro-Wedge
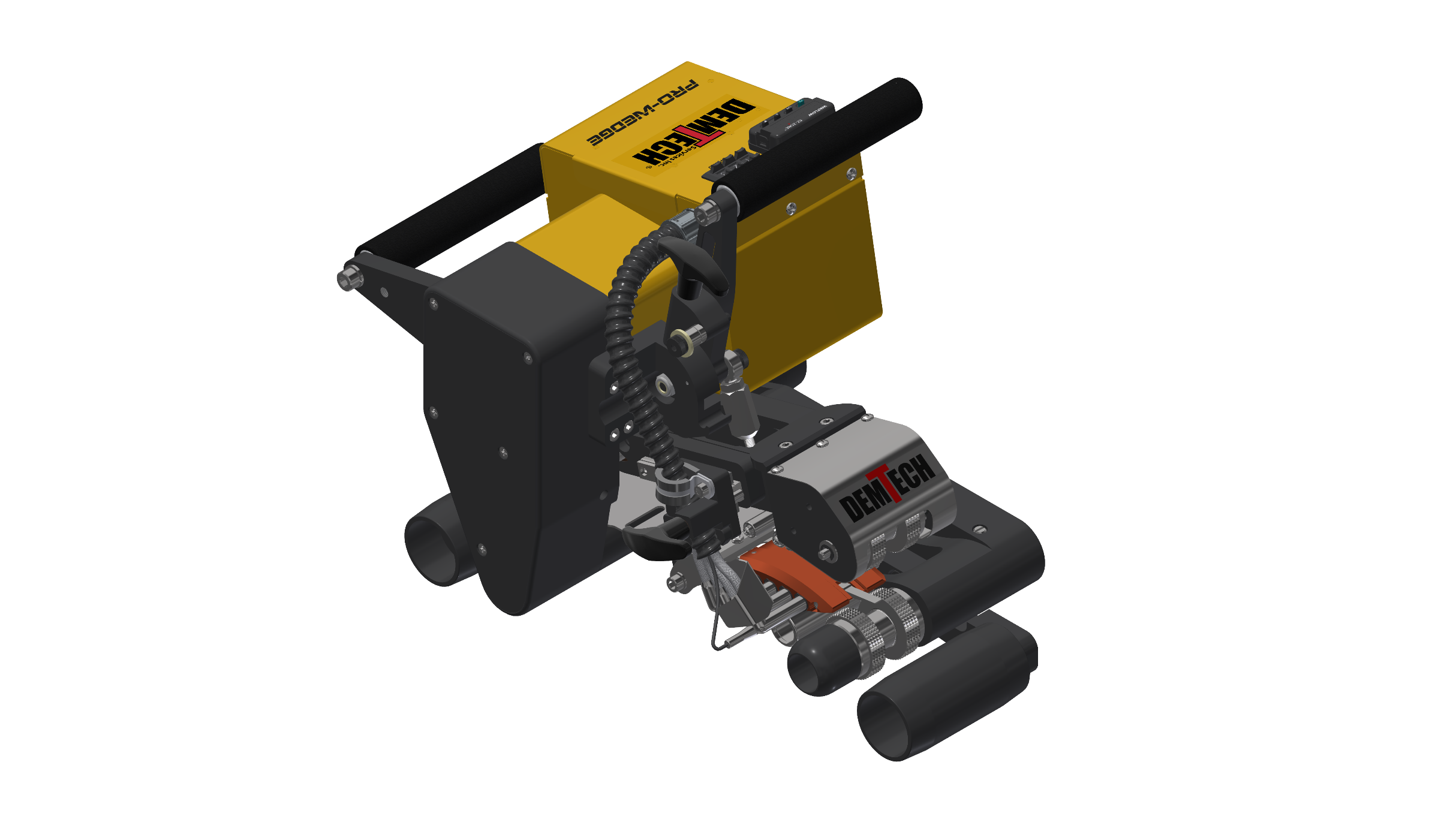
VM-20 Operator’s Manual
Model Number: VM-20/A
Revision: F
© Copyright 2020 by DEMTECH Services, Inc.
All Rights Reserved
Scope of Manual:
This manual contains procedures for safety, general unpacking,
set-up, and operation of your DEMTECH Services, Inc. Pro-Wedge VM-20.
The text of this publication, or any part thereof, may not be reproduced or transmitted in any form or by any means, electronic or mechanical, including photocopying, recording, storage in an information retrieval system, or otherwise, without prior written permission of DEMTECH Services, Inc.
Notice
Patents have been granted and/or patent applications are pending or are in the process of preparation on all DEMTECH Services, Inc. developments.
The material in the manual is for informational purposes only and is subject to change without notice.
DEMTECH Services, Inc. assumes no responsibility for any errors that may appear in this manual.
Manual Number: 100-OPERATOR’S MANUAL/VM-20/AU, Revision: F
DEMTECH Services, Inc.
6414 Capitol Avenue Diamond Springs, CA 95619 U.S.A.
Telephone: (530) 621-3200
Toll Free: (888) 324-9353
Fax: (530) 621-0150
Table of Contents
1 Safety Precautions………………………………………………….Page 2
2 General Safety Information……………………………………page 3
2.1 Intended Use…………………………………………………………Page 3
2.2 Maintenance…………………………………………………………Page 3
3 General Product Data……………………………………………..page 4
4 Operating Environment……………………………………………page 4
5 Site Preparation………………………………………………………page 4
6 Unpacking & Installation Instructions……………………page 5
6.1 Unpacking and Preparation………………………………………….Page 5
6.2 Electrical Plug Connection…………………………………………..Page 6
6.3 Generator Recommendations………………………………………..Page 6
6.4 Accessories…………………………………………………………..Page 7
7 Material Set-up………………………………………………………..page 8
7.1 Set-up Nip Pressure Adjustment…………………………………….Page 9
7.2 Set-up Upper Contour Roller Configurations:……………………..Page 11
7.3 Set-up Lower Contour Roller Adjustment…………………………Page 14
8 Welding Procedure………………………………………………..page 18
8.1 Power Up…………………………………………………………….Page 18
8.2 Setting Wedge Temperature…………………………………………Page 18
8.3 Setting Weld Speed………………………………………………….Page 19
8.4 Starting a Weld………………………………………………………Page 21
8.5 Ending a Weld……………………………………………………….Page 21
8.6 Shut-Down……………………………………………………………Page 21
9 Reference Documents………………………………………………page 22
9.1 Appendix A…………………………………………………………..Page 24
9.2 Appendix B……………………………………………………………Page 25
9.3 Appendix C……………………………………………………………Page 26
Safety Precautions
Safety precautions for operating personnel and equipment:
WARNING 1: Operating personnel should perform only the procedures described and recommended in this manual. Only qualified service personnel familiar with electrical shock hazards and mechanical entanglement hazards present inside the equipment should perform disassembly or corrective maintenance of the equipment.
WARNING 2: To avoid shock hazards, the equipment must be grounded with an adequate earth ground in accordance with local and national electrical codes.
WARNING 3: The locations of potentially dangerous voltages and other hazards are identified and labeled on the equipment. Be careful to observe these warnings when installing, operating, maintaining or servicing the equipment. Observe all warnings in this manual.
WARNING 4: Make sure to turn off the equipment power and remove the ~ (ac) line cord from the power outlet before attempting to service the equipment. Do not perform service unless you are qualified and trained to do so.
CAUTION 1: Observe the precautions given on the equipment and within this manual to prevent damage to the equipment.
CAUTION 2: Before connecting the equipment to its electrical power source, check that the ~ (ac) voltage, frequency and current to be supplied to the equipment are correct and match the serial plate affixed to the system.
CAUTION 3: Use proper handling and packaging procedures for Electro-Static Discharge (ESD) sensitive circuit boards. Assume that all circuit boards are sensitive to potential damage from ESD.
CAUTION 4: Unauthorized personnel should not remove from the equipment those panels or covers that are provided for protection and/or require a tool to remove.
General Safety Information
The DEMTECH Services, Inc. Pro-Wedge VM-20 Wedge Welder, hereinafter referred to as the Pro-Wedge or welder, is a high temperature and voltage piece of equipment. Always disconnect the power source before performing any service and/or maintenance procedures on the welder. Never lift, pull or carry the welder by the power cord or electrical connection. Always maintain slack in any extension cords connected to the welder while in operation to avoid damage to the power connections. At all times while operating the welder keep hands, fingers and other body parts well clear of the heating element and related mounting components. Always use the Pro-Wedge in a well-ventilated area when welding materials such as PVC which can produce toxic fumes. Do not inhale toxic fumes when present. Do not operate near flammable materials of any kind. Do not apply flammable materials, including liquids, to seam area. Allow welder to cool to room temperature, at least 15 minutes, before returning to the shipping/storage case. Protect welder from exposure to rain or standing water. Never attempt to weld in standing water.
Intended Use
For additional product information please refer to the product data sheet located in Appendix C of this manual.
The Pro-Wedge has been manufactured according to the latest technology and current safety regulations. However, improper use or abuse may lead to hazardous conditions for the user or third party or damage to the unit.
Always have this manual handy at the location where the Pro-Wedge is being used so that it can be referred to quickly and easily.
The technician assigned to operate this welder must have read through and become familiar with this manual before starting work, particularly the section on safety.
Do not make changes or modifications to the Pro-Wedge relative to safety without contacting the manufacturer for advice.
Maintenance
Maintenance, inspection and adjustment of the Pro-Wedge may only be carried out by qualified personnel. Before removing or installing spare parts or performing other repair operations to the Pro-Wedge, consult the manufacturer for advice on proper procedures. This will help insure a safe and successful outcome. Always make sure all screw connections are tight before attempting to operate the unit after maintenance or repair. Also make sure all covers, guards, and other safety devices have been reinstalled before use.
General Product Data
The DEMTECH Services, Inc. Pro-Wedge VM-20 Geo-Membrane Wedge Welder, hereinafter referred to as the Pro-Wedge or welder, dramatically speeds the welding of plastic sheet materials through the use of its wedge heating elements and multiple pressure roller design. These features combined with state-of-the-art electrical and electronics controls and an easy to use User Interface (UI) makes performing welding tasks very efficient. The semi-automated operation of the welder eliminates cumbersome setup and speeds up processing time while providing a very rugged and reliable welder. The enclosed controller sub-system is easy to maintain. You can be assured the Pro-Wedge has been built using the highest quality materials available which include Billet Aluminum and ground and hardened steel. DEMTECH Services, Inc. strives to make our welders easy to use and built to last. Just like all other DEMTECH Services, Inc. products, even a first time user will be productive in minutes.
Operating Environment
The Pro-Wedge is intended to be operated within the following environmental ranges and conditions. Operating the welder in environments which are less than or greater than the nominal values listed can adversely affect performance.
Temperature +32 to +100° Fahrenheit (F); 74° F Nominal
(+0 to +38° Centigrade (C); 23°C Nominal)
Humidity 0 to 90% (non-condensing); 45% Nominal
Elevation 0 to 7,000 Feet; 2,000 Feet Nom
(0 to 2,134 meters; 610 meters Nominal)
Site Preparation
Before proceeding with the unpacking and installation instructions in the following section(s) make sure the work site is prepared and ready to use the Pro-Wedge. You should have an adequate power source capable of providing clean Alternating Current (AC) power at 110 or 220 Volts at the rated current. Refer to the serial plate (P/N 100-399) affixed to the back side of your welder for the voltage and current requirements. The install and use area should be clean, dry and free of debris and provide adequate working area to allow efficient and effective use of the welder.
Unpacking & Installation Instructions
This section contains instructions for the unpacking, placement and installation of the Pro-Wedge. Carefully review the following information, sub-sections and each procedure before beginning unpacking and installation of the welder.
The Pro-Wedge comes complete in a sturdy, reusable, portable shipping/storage case. The custom foam inserts protect the welder from damage during shipping and storage and should always be left inside the case. When the welder is out of the case, make sure to keep the lid closed to avoid dirt, dust, debris and/or water from getting inside. The welder must be removed from the case and placed onto the work site for use. When not in use, the Pro-Wedge should always be stored in the shipping/storage case to protect it from the elements and potential damage.
Note: The welder illustrated in this manual shows ALL available features for the
Pro-Wedge, therefore, your welder may vary slightly in appearance from that depicted.
Unpacking and Preparation
- Before opening the shipping/storage case for the first time and unpacking the welder, inspect the outside of the case thoroughly for any signs of mishandling or damage during shipping. Report any damage to the shipping carrier immediately and do not proceed with unpacking. You should consult your administration concerning claims for shipping damage. Please notify DEMTECH Services, Inc. or your authorized DEMTECH distributor where the product was purchased in the event of any shipping damage.
- Unlatch and open the shipping/storage case lid and inspect inside the case and the welder thoroughly for any signs of mishandling or damage during shipping. Report any damage to the shipping carrier immediately and do not proceed with unpacking. You should consult your administration concerning claims for shipping damage. Please notify DEMTECH Services, Inc. or your authorized DEMTECH distributor where the product was purchased in the event of any shipping damage.
- Make note of the orientation of the welder and packing foam inserts inside the shipping case to facilitate repackaging the welder after use.
- To avoid injury to personnel and/or damage to the welder, be sure to use adequate care when lifting and removing or lowering and replacing the welder into the shipping/storage case.
- The welder must be removed from the shipping/storage case and placed in an appropriate location suitable for the welding you intend to perform.
Electrical Plug Connection
The Pro-Wedge is supplied with an appropriate U.S. plug-end according to the specified
operating voltage of the welder. The supplied plug-end can be replaced by the customer
as long as the new one is rated at a minimum of 20 amps.
This procedure should only be performed by a qualified electrician.
Electrical Extension Cords
Extension cords should be at least 12 gauge and regardless of overall length should have a minimum of 3 plug-end connections.
Conductor Size | 3-Wire
10 AWG (5.3 mm2) |
3-Wire
12 AWG (3.3 mm2) |
Length | 500 Feet
(152 meters) |
250 Feet
(76 meters) |
Table 6.2 Maximum recommended extension cord lengths.
Generator Recommendations
When operating the Pro-Wedge using house power from a building circuit use the appropriate plug and power cord configuration. When in-field generators are used they must be rated for a minimum of 5,000 watts, however a rating of 6,500 watts or more is highly recommended in order to obtain the best welder performance and temperature control. As a rule, higher wattage generators provide better welder performance. Keep in mind that the length and wire gauge of any extension cord being used combined with the capacity of the generator ultimately determines the operating voltage and therefore welder performance.
Accessories
The Pro-Wedge has been designed to weld a wide range of materials on most sub grade types. However, for the best results on each job site, there are many different accessories available to help make the welding process easier. For example, the independent front travel rollers can be replaced with a wide tubular roller to help prevent sand and loose dirt from pushing up onto the bottom sheet of material. For extreme cases of sandy sub grades, an outrigger system and raised rear travel roller are available. Please contact supplier for more information and pricing.
Material Set-up
The Pro-Wedge is designed to weld a wide range of material types and thickness’ from very thin PE, PP and PVC to very thick materials such as 60-120 Mil (1.5-2.5mm) HDPE. Non-woven geotextiles can also be welded at very high speeds (up to 32 ft/minute with stock motor). The Pro-Wedge uses a spring-loaded upper contour roller system and “floating” wedge design that allows the operator to weld several different thicknesses of material without resetting the adjustments. However, for best results on all materials, the following set-up procedure can be used.
Note: before you begin, you will need the following items to set-up a Pro-Wedge hot wedge welder:
- Adjust material using the material set up template as seen in Figure 7.1 (P/N 100-160T). Trace the template on a piece of the material you will be welding, cut it out and write the word “Top” on your adjustment material at the same location that it appears on the template. Fold adjustment material so that the word “top” is visible.
- Set of metric Allen wrenches.
- 13mm open end wrench.
- Phillips screw driver.
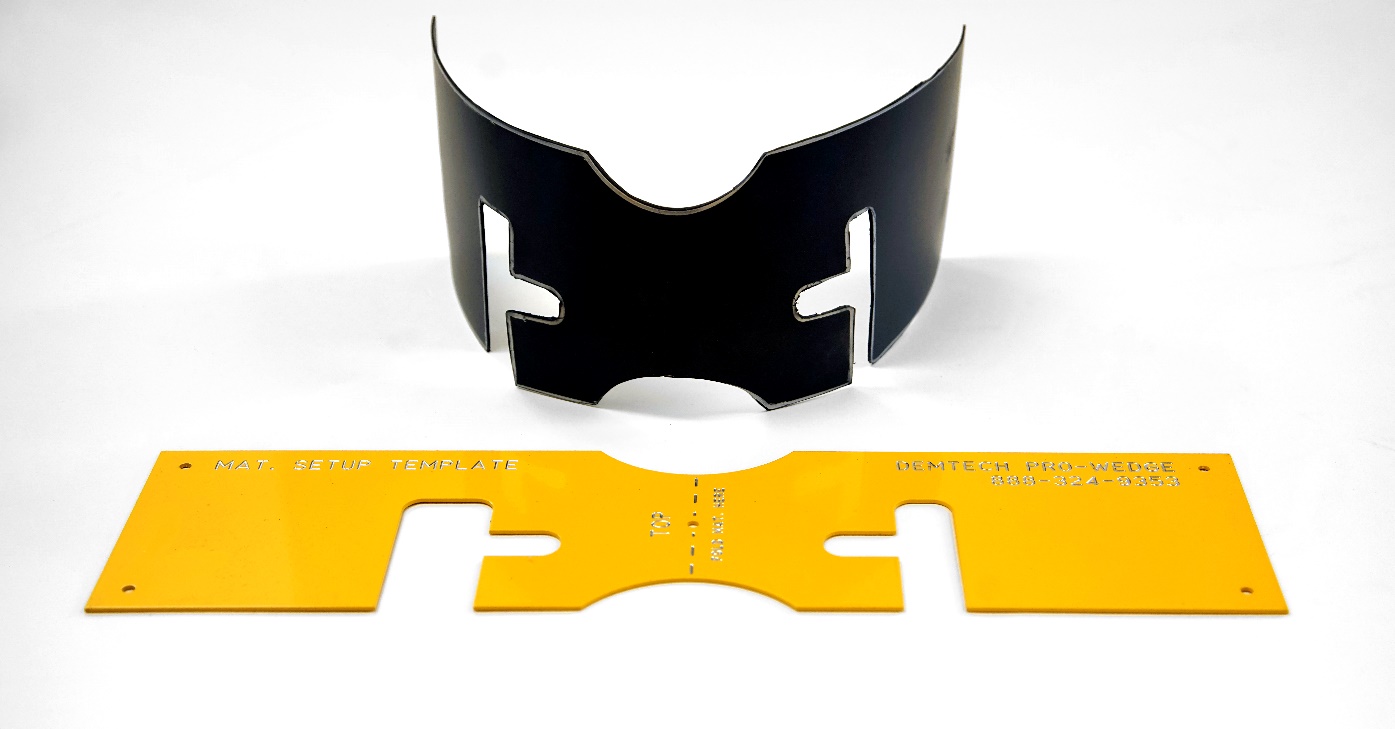
Set-up Nip Pressure Adjustment
Adjustment Location:
The nip pressure adjustment is located between the nip lever and upper nip arm; it is a hex shaped turnbuckle style nut (#11, Figure 7.2).
The correct amount of nip pressure is needed to get a good weld. It is also important that the nip rollers are providing enough traction to keep the Pro-Wedge from “burning out”. This can happen when the nip rollers lose traction and spin on the material, causing the Pro-Wedge to stop in the seam and burn a hole in the material.
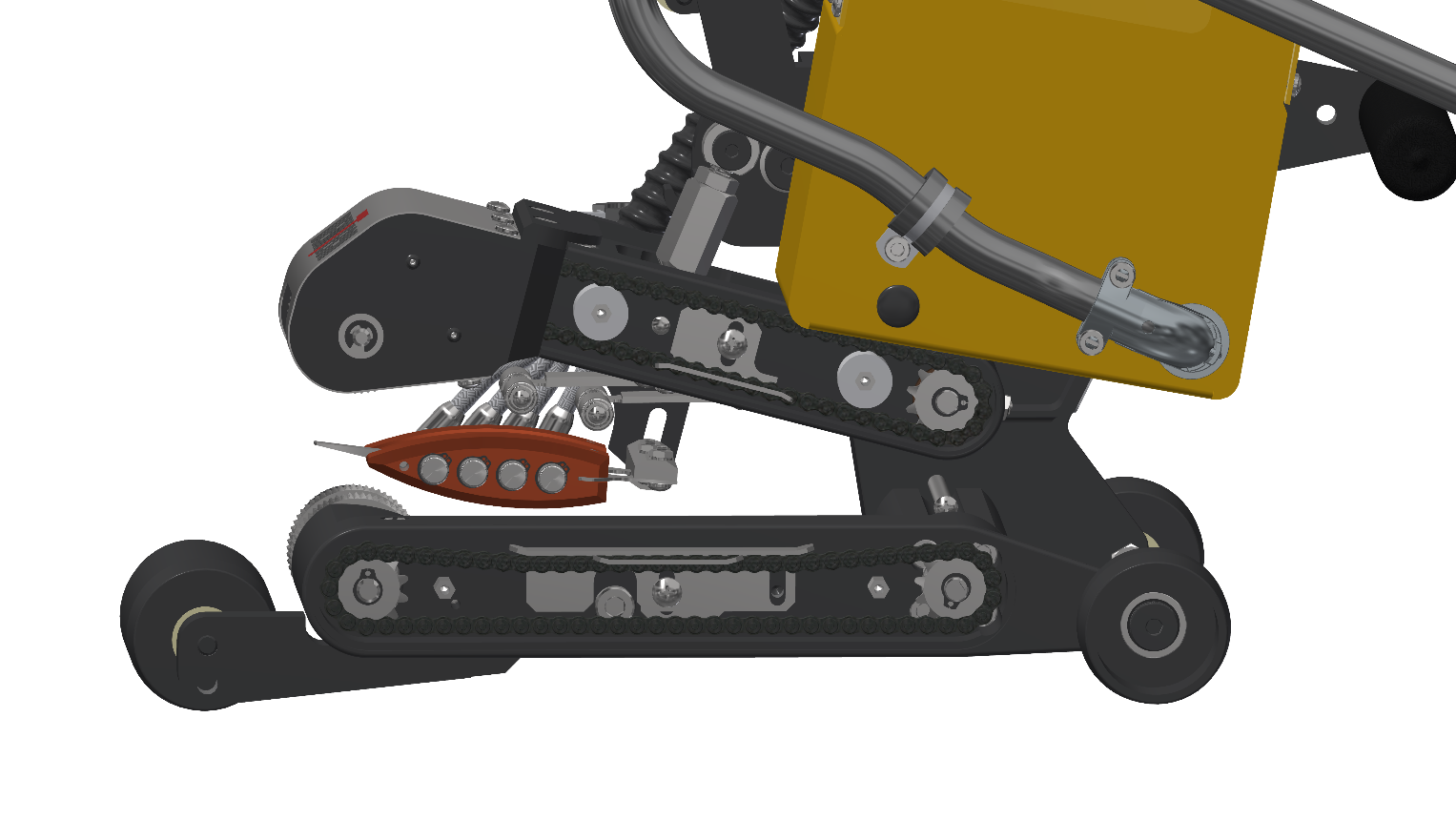
Figure 7.2
Note: Pressure Adjustment for thin material and geotextiles:
These materials require less nip pressure. Too much pressure can cause
the material to perforate at the edge of the seam causing a “zipper” effect.
Make sure the heating wedge (#7, Figure 7.2) is in the disengaged position.
Turn the nip pressure adjustment hex nut (#11, Figure 7.2) clockwise while looking down from above several turns, raising the nip arm up to give a fresh starting point for this adjustment. (Loosen set screw(s) on hex nut first if present to avoid damaging threads on eye bolts)
Place one end (one thickness) of your adjustment material between the nip rollers and into the unit about 1” inch. Engage nip rollers by pushing down on the nip lever until it has “clicked” into place and is held in position by the lock pin. At this point the material should move around freely between the nip rollers.
Turn the hex nut (#11, Figure 7.2) counter clockwise until the nip rollers begin to pinch down on the material and you cannot turn the nut by hand anymore. This zeroes the adjustment.
Disengage nip rollers and turn the hex nut counter clockwise one full rotation.
Insert the adjustment material (the opposite end of the fold, two thicknesses) between the nip rollers and engage nip rollers together until the lock pin clicks into its detent as shown on the next page (Figure 3). Check pressure by attempting to move the material side to side. If you are able to move the material or pull the material straight out without the nip rollers turning, disengage the nip pressure and turn adjustment nut (#11, Figure 7.2) counter clockwise ¼ turn at a time until the desired pressure is reached. Remember to tighten the set screw(s) on the adjustment nut after you have completed adjustment of the nip pressure to prevent the pressure from backing off while welding.
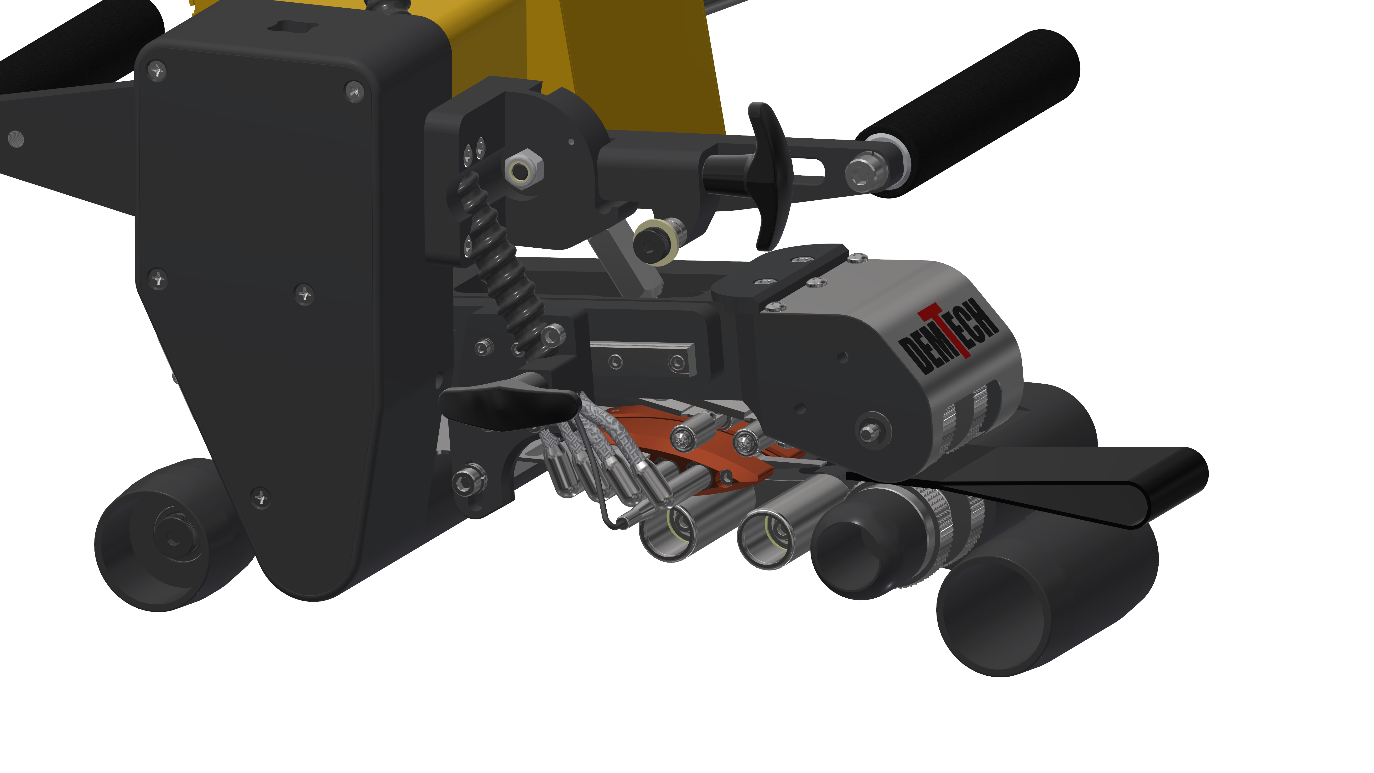
3
Note: When the nip pressure adjustment is set correctly, engaging the nip pressure lever should take some effort but it should feel like a smooth motion. Again, it is important that you are getting enough traction to avoid burning out and at the same time providing enough nip pressure to create a good weld. Keep in mind that the thicker the material being welded and especially textured material, the greater the pressure should be.
Set-up Upper Contour Roller Configurations:
You can skip this step and proceed to Section 7.3
on page 14 if the spring/roller configuration is already
correct for the material you will be welding!!!
For specific applications of the material you will be welding refer to the Upper Contour Roller Assembly Spring Configuration Chart on the following page.
Refer to Figure 4 for an example of an upper contour roller assembly recommended for HDPE welding.
Location:
The upper contour roller assembly is located above the heating wedge and is fixed to the bottom of the nip arm assembly. Adding or removing the flat leaf springs will increase or decrease the upper contour roller tension. For materials not shown on chart, contact DEMTECH for recommendation.
Note: There are two types of springs, one that the roller axle mounts to and one that is used as a stiffener or “back up spring”. There are also two mounting locations on the mount plate (#3, Figure 4), one for the rear roller set (closest to the nip rollers) and one for the front roller set (furthest from the nip rollers).
Upper Contour Roller Assembly Spring Configuration Chart:
Material | Thickness | Rear Set Installed | Front Set Installed |
HDPE / LLDPE | 40-120 mil | Yes w/two backup springs | Yes w/one backup spring |
HDPE / LLDPE | 20-30 mil | Yes w/one backup spring | No |
PP Non-Reinforced | 20-40 mil | Yes w/no backup spring | No |
PP Reinforced | 30-45 mil | Yes w/no backup spring | Yes w/no backup spring |
PVC | 50-100 mil | Yes w/no backup spring | No |
PVC | 20-40 mil | Yes (light spring # 100-012A) | No |
Geotextiles | 4-50 oz. / sq. yd. | Contact Manufacturer | Contact Manufacturer |
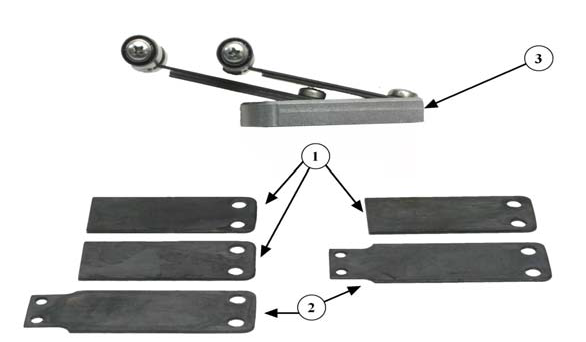
Figure 4
Figure 4 shows the triple / double assembly configuration for welding 40-120 mil (1.0-2.5mm) HDPE / LLDPE material. For reference Item 1 is P/N 100-010, Item 2 is P/N 100-012 (P/N 100-012A is light version).
Changing spring configuration:
Removing-upper contour roller assembly:
Remove screw from the end of the shaft that the material guide plate (#12, Figure 2) pivots on, then slide material guide off of shaft and set aside.
Remove the two Phillips head screws that attach the upper contour roller assembly mount plate (#1, Figure 5) to the nip arm and remove contour assembly from the unit. You may need to move the heating wedge fore or aft for access with screwdriver.
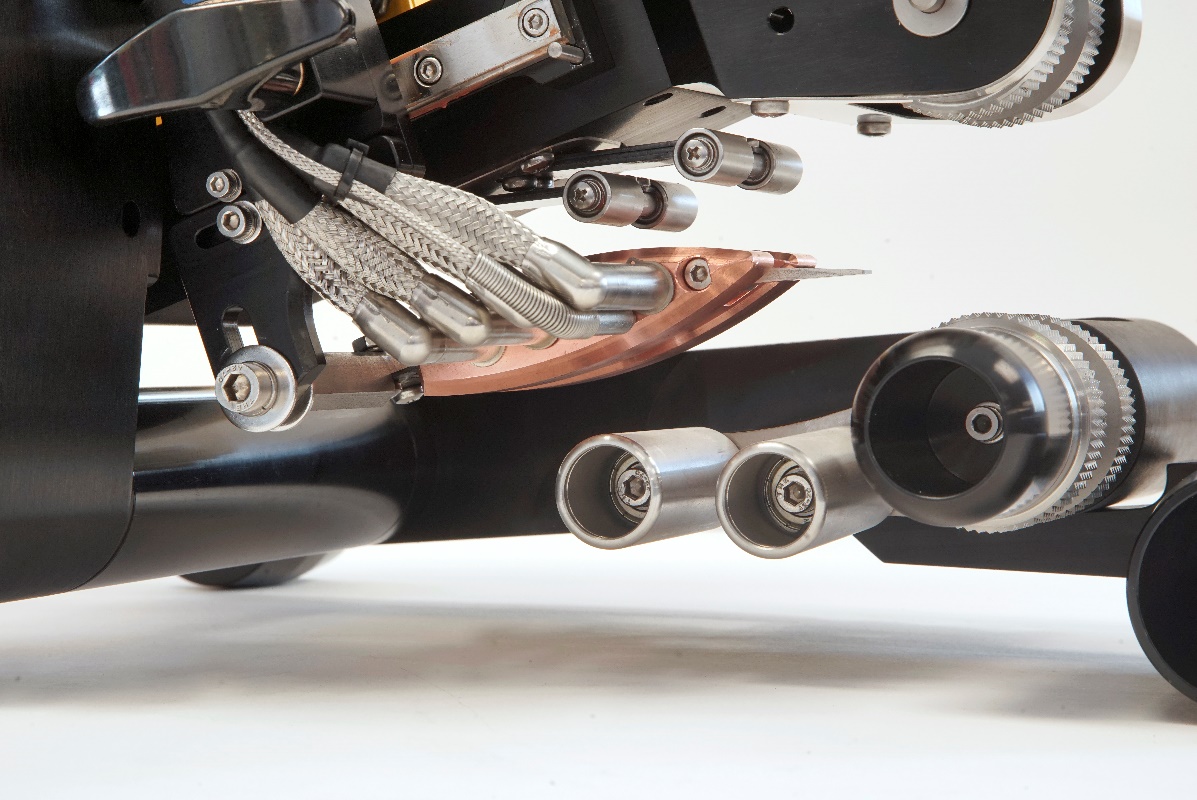
5
The individual upper contour rollers and springs can now be configured to match the material you will be welding. See the Upper Contour Roller Assembly Spring Configuration Chart on the previous page.
Set-up Lower Contour Roller Adjustment
Location:
The lower contour rollers (#3 and #4, Figure 6) are located below the heating wedge and are mounted to the lower frame directly in front of the lower nip roller (#2, Figure 6). For this adjustment you will need a 13mm open end wrench and a 4mm and 6mm Allen wrench.
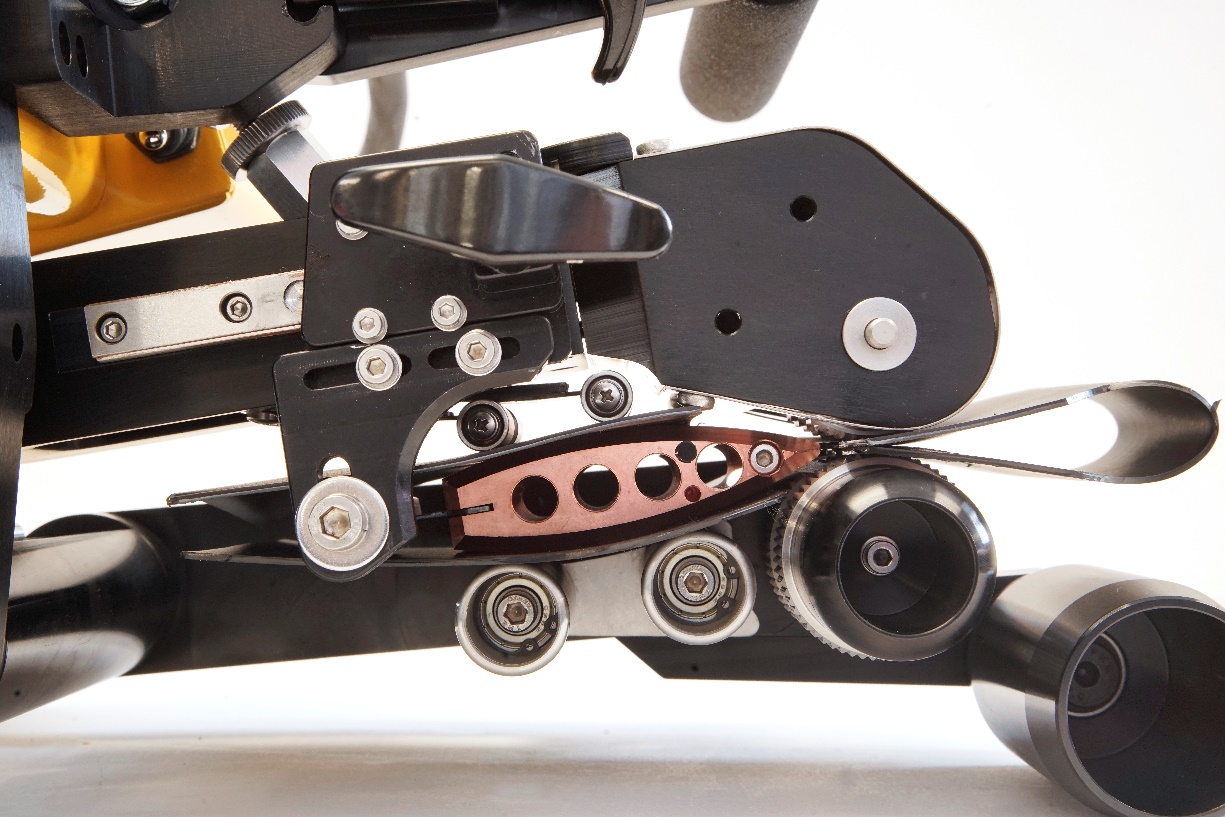
6
With the nip pressure lever in the up position and the wedge in the disengaged position, insert the adjustment material that you cut earlier from the template into the Pro- Wedge as shown in Figure 6 above:
Make sure the word “Top” is facing up then slide the material above and below the wedge and between the upper and lower contour rollers as shown above. Insert just enough in so that about 2 ¾” (70mm) of material is protruding out of the nip rollers from the point where the nip rollers pinch down on the material. Slide the wedge to its engaged position until it locks into its detent. Then lock the nip pressure lever down on to the material.
Note 1: Make sure if using a split wedge with an air channel pin, that the notch is cut in the end of the doubled-up piece of material as it is detailed on the material template. This is to allow clearance for the air channel finger when the material set-up piece is in place.
With a Phillips screw driver remove lower frame chain cover to expose the lockdown bolt for the front lower contour roller (#4, Figure 6).
Using a 6mm Allen wrench, loosen the lockdown bolt and then temporarily adjust the front lower contour roller down, clockwise, away from the wedge using a 4mm Allen wrench on the end of the roller (this will give you a fresh starting point and you will make a final adjustment on this roller later).
Using a 13mm open end wrench, loosen the lockdown bolt (hex head) for the rear lower contour roller (#3, Figure 6). You can now adjust the height of the wedge by adjusting the rear lower contour roller up or down with a 4mm Allen wrench at the end of the roller. Once the desired position has been achieved, tighten the lockdown bolt (hex head) then check the adjustment again to make sure it did not move when tightened.
Note 2: The most important adjustment is the positioning of the wedge in relationship to the lower nip roller (#2, Figure 6). The distance between the lower tip of the heating wedge and the lower nip roller should be slightly more than the thickness of the material you will be welding. The distance is set by adjusting the rear lower contour roller (#3, Figure 6) up or down.
Note 3: When adjusting the lower contour rollers (#4) and (#3) rotate them both to the right (counterclockwise) and up so that in their adjusted positions the rollers are closest to the nip roller (#2). Also because the rear contour roller (#3) is forcing the wedge up against the upper contour roller spring tension, you may notice the roller will still spin with your fingers. This is normal. The amount of resistance of the roller when turning it with your fingers does not matter.
Note 4: The lower contour rollers are mounted to the lower frame on eccentric cams that thread onto the lockdown bolts. When adjusting, you may need to work the 4mm Allen wrench and the 6mm Allen wrench for the front contour roller (4)) or the 13mm open end wrench for the rear contour roller (3)) simultaneously to rotate the roller smoothly.
Warning! If the rear lower contour roller is adjusted too high, there will not be enough clearance for the top sheet to travel through the welder and it will be pinched between the top of the heating wedge and the upper nip frame. This will result in loss of welding nip pressure and an inconsistent weld.
Adjust the front lower contour roller (#4, Figure 6) up and to the right (counterclockwise) until it just comes in contact with the material. The roller should have a slight amount of resistance as you rotate it. If you adjust it to tight it will rock the wedge and change the rear roller (#3) adjustment.
Note 5: If you are setting up the Pro-Wedge to weld thin material or in very hot ambient conditions the front contour roller (#4) adjustment should be set very loose or backed off completely to reduce material dwell time (over heating material) and minimize the possibility of burn outs.
Step 4: Set-up Wedge Fore/Aft Adjustment
The fore/aft adjustment sets the limit of travel of the heating wedge in its fully engaged position. In other words, how close the tip of the wedge is to the nip rollers. If the tip of the wedge is too close to the nip rollers they will pinch down on the wedge when pressure is engaged, reducing the amount of nip pressure on the heated material. This can also cause damage to the tip of the wedge when running out of the end of the seam.
There are two types of wedge slide lock mounts, the old style one-piece (Item 1 in Figure 7, P/N 100-200) and the new style two-piece (Item 3 in Figure 7, P/N’s 100-200L and 100-200U) as shown in Figure 7. The two-piece configuration is also shown in Figure 6. If necessary units with the old style one-piece mount can and should be upgraded to the new style two-piece mounts.
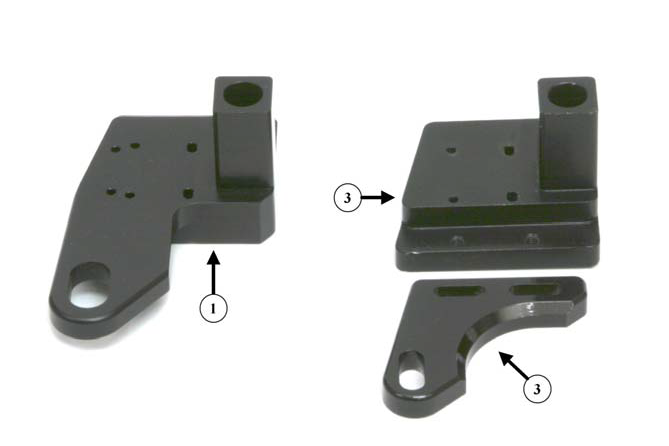
7
Adjustment procedures for one-piece lock mount assemblies (#1, Figure 7):
With the material set-up piece in place and with the nip lever and wedge engaged as shown on Figure 6, use a 5mm Allen wrench to loosen the wedge mount bolt that connects the wedge hex mount to the wedge slide lock mount (#1, Figure 7).
Move the heating wedge forward or backward (left or right) so that there is plenty of clearance between the tip of the wedge and the upper and lower nip rollers. When adjusting Pro-Wedge for welding HDPE, position the lock bolt as far down and forward (left) in the oval adjustment slot as possible.
Tighten lock bolt to set adjustment.
Adjustment procedures for two-piece lock mount assemblies (#3, Figure 7):
With material set-up piece in place and with nip lever and wedge engaged as shown on Figure 6, use a 5mm Allen wrench to loosen the wedge mount bolt that connects the wedge hex mount to the lock mount (#3, Figure 7). For HDPE set-up, position lock bolt as far down in slot as possible and tighten bolt.
Using a 3mm Allen wrench, loosen the two lock screws that hold the lower piece of the assembly to the upper piece. You will need to insert the 3mm Allen wrench between the cartridge heater lead wires to access one of the screws.
Move the heating wedge forward or backward (left or right) so that there is plenty of clearance between the tip of the wedge and the upper and lower nip rollers. When adjusting Pro-Wedge for welding HDPE the tip of the wedge should have the same clearance as shown in Figure 6.
Tighten lock screws to set adjustment. Re-check all adjustments to make sure they are correct before disengaging nip lever and wedge and removing material set-up piece.
When in doubt, contact DEMTECH!
(888) 324-WELD (9353)
(530) 621-3200
(530) 621-0150 fax
Welding Procedure
Power Up
Connect the Pro-Wedge power cord to power source making sure that the voltage is correct for the model of welder you have. Please refer to Sections 6.2, 6.3, Error! Reference source not found. and Error! Reference source not found. on page 6 and Error! Bookmark not defined. of this manual for details.
Flip the main power toggle switch (#4, Figure 8) to the “on” position (up). The main power switch is located on the front of the control box, below the front handle. After a 3 second delay, the temperature control unit (#1, Figure 8) located on top of the control box should light up and display current wedge temperature.
Turn on the drive motor with the motor switch (#3, Figure 8), located on rear of the control box, near the nip pressure adjustment hex nut. It is recommended that the drive motor remain on at all times while the welder is plugged in. This helps to eliminate hot spots on the nip rollers and makes starting a weld quicker and easier.
Setting Wedge Temperature
Watlow EZ-Zone Controller (4 button style)
The EX-Zone temperature controller has a dual display. The current wedge temperature set point is displayed on the right side of the display. The actual wedge temperature is displayed on the left side of the display.
To adjust the wedge temperature set point, press the up arrow button to increase the set point or the down arrow button to decrease the set point. (Refer to the Welding Speed/Temperature Chart, Appendix A, for recommended wedge temperature settings).
Watlow 935 Controller (3 button style)
To display the current wedge temperature set point, press and hold the blue “set” button located on the temperature controller. To adjust the set point, press up or down arrow buttons while holding down the “set” button. (Refer to the Welding Speed/Temperature Chart, Appendix A, for recommended wedge temperature settings).
Setting Weld Speed
To set weld speed, use “+” and “-“ buttons on speed setting pot (#2, Figure 8) located on top of control box, next to temperature control unit. Keep in mind that the three-digit number on the speed setting pot does not relate directly to feet or meters per minute. (Refer to the Speed Setting versus Actual Travel Rate Chart, Appendix B, for setting versus feet per minute values).
Note on High/Low Gear: Unless otherwise specified, your Pro-Wedge has been factory set in low gear, which gives the welder a speed range of 0-18 feet per minute (0-5.5 meters/min). You will use this range for most all in-field geomembrane welding applications and especially ones that require high torque such as HDPE. The main motor drive sprockets on the Pro-Wedge can be flipped to change the ratio to high gear, changing the speed range to 0-32 ft/min (0-9.5 meters/min) for high speed seaming of thin materials and non-woven geotextiles. Speed versus setting values are listed for high and low gear in the speed-setting chart in Appendix B.
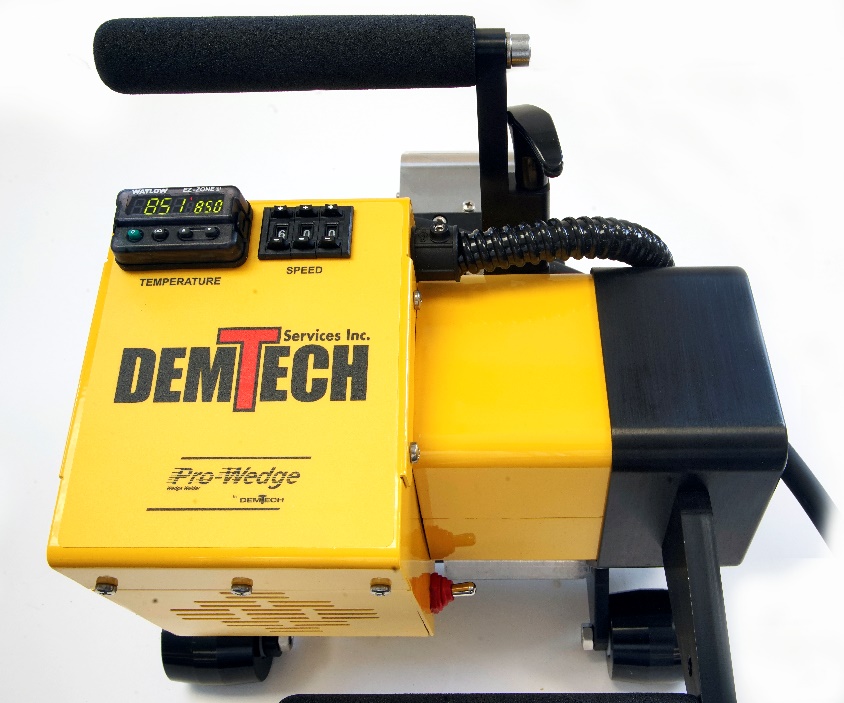
8
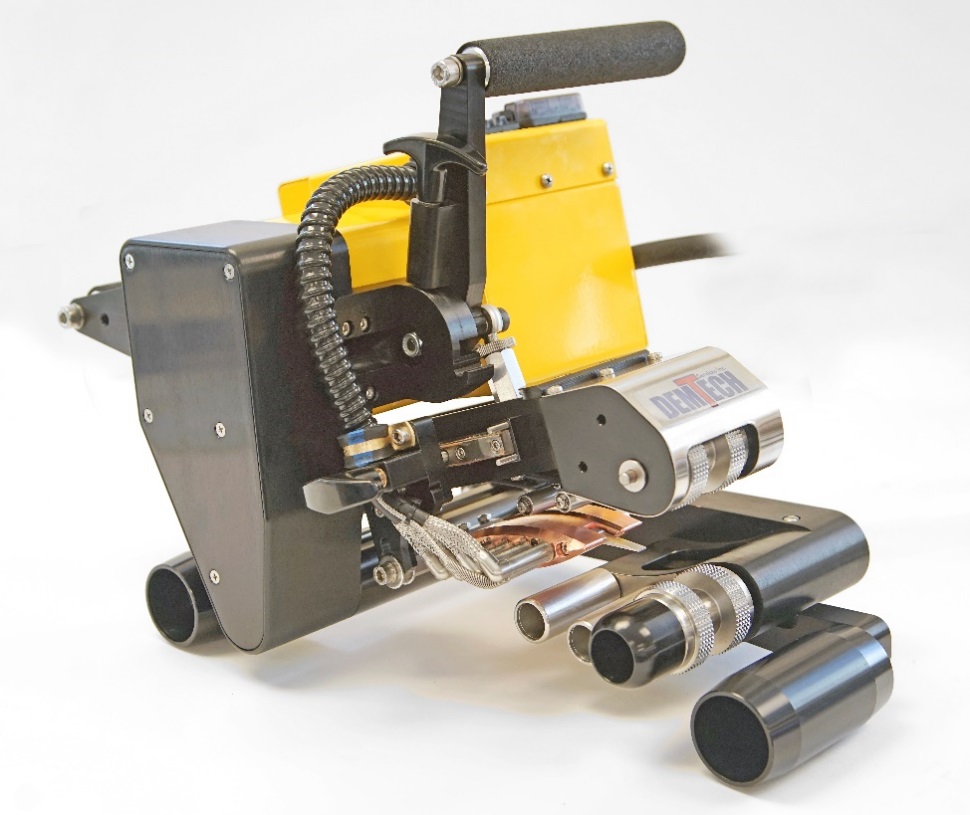
Figure 9
Starting a Weld
To start a weld, you must first make sure that the material to be welded is set at the proper overlap. The optimum overlap is 5-6 inches (12.7-15.2 cm) for field welds. For recommendation on in-house fabrication overlap settings, please contact the manufacturer.
Start the loading process with the nip lever in the “up” or disengaged position, the heating wedge in the “forward” or disengaged position (Figure 9), and the motor on with the nip rollers turning.
First, peel back the top sheet to expose the bottom sheet. Load bottom sheet of the material into welder, between both lower contour rollers and the bottom of heating wedge, then between the two nip rollers.
Second, insert the top sheet into the welder, between the upper contour roller(s) and the top of the heating wedge, and then between the nip rollers. You may need to roll the welder forward and backward a little for both sheets to settle into the welder.
Third, pull out on the wedge lock handle and slide wedge toward nip rollers until the lock pin slides off the end on the slide rail. Make sure wedge is completely engaged before continuing.
Fourth, engage nip rollers by pushing the nip pressure lever down until it “clicks” and is locked in position. At this time the welder should be moving and welding on its own. If the nip rollers are spinning on the material and burning a hole, quickly disengage nip rollers, roll the welder down the seam a few more inches, past the overheated area, and engage again.
Ending a Weld
Just as the welder is about to run out of the end of the seam, disengage nip rollers, slide welder out of the seam, and then disengage wedge. At this time it is a good idea to tip the Pro-Wedge up onto the front handle, raising the back of the unit, to prevent a hole being melted in the material from heat radiating from the wedge.
Shut-Down
To shut down the Pro-Wedge, simply turn main power switch to the “off” position or unplug unit. After 5-10 minutes, place unit in shipping/storage case provided with welder.
Note: Practice makes perfect.
Reference Documents
Appendix A, Welding Speed / Temperature Chart
Refer to Appendix A for recommended preliminary speeds and temperatures for a wide range of material types and thicknesses. This chart is a great reference tool, however all site conditions are different and the settings recommended on the chart may not be suitable for your specific site. Please contact a DEMTECH technical representative for advice on appropriate settings.
Appendix B, Speed Setting versus Actual Travel Rate Chart
Refer to Appendix B for a chart showing the travel (welding) speed of the Pro-Wedge at various speed pot settings. Keep in mind that actual speed, especially at the highest setting (999) may vary depending on power supply, length of cords, etc.
Appendix C, Pro-Wedge Product Information Sheet
Refer to Appendix C for a product brochure showing photos and technical specifications of the Pro-Wedge.
Appendix D, Pro-Wedge Product Warranty
Refer to Appendix D for the DEMTECH product warranty.
Appendix E, Pro-Wedge Spare Parts Identification
Refer to Appendix E for the spare parts identification diagrams and DEMTECH part number listings for ordering potential wear item replacement parts for the Pro-Wedge. When ordering be sure to specify the DEMTECH Part Number not the Item Number.
END OF OPERATOR’S MANUAL
This page is intentionally without content.
Appendix A
Pro-Wedge Welding Speed / Temperature Chart
Material Type | Thickness
mil (mm) |
Ambient
Temperature |
Wedge
Temperature |
Maximum Welding
Speed ft/min (m/min) |
Solid
Wedge |
Split
Wedge |
Solid
Nips |
Split
Nips |
Upper
contour rollers |
HDPE | 12 (0.3) | 65-85 F (18-30 C) | 650 F (340 C) | 32 (9.8) | X | rubber | single light upper | ||
HDPE | 20 (0.5) | 65-85 F (18-30 C) | 750 F (400 C) | 25 (7.6) | X | rubber | single upper | ||
HDPE | 30 (0.75) | 65-85 F (18-30 C) | 750 F (400 C) | 18 (5.5) | X | rubber | single upper | ||
HDPE | 40 (1.0) | 65-85 F (18-30 C) | 750 F (400 C) | 16 (4.9) | X | steel | double/triple | ||
HDPE | 60 (1.5) | 65-85 F (18-30 C) | 860 F (460 C) | 15 (4.6) | X | steel | double /triple | ||
HDPE | 80 (2.0) | 65-85 F (18-30 C) | 860 F (460 C) | 13 (4.0) | X | steel | double/triple | ||
HDPE | 100 (2.5) | 65-85 F (18-30 C) | 860 F (460 C) | 12 (3.7) | X | steel | double/triple | ||
HDPE | 120 (3.0) | 65-85 F (18-30 C) | 860 F (460 C) | 8 (2.4) | X | steel | double/triple | ||
LLDPE | 20 (0.5) | 65-85 F (18-30 C) | 600 F (315 C) | 25 (7.6) | X | rubber | single upper | ||
LLDPE | 30 (0.75) | 65-85 F (18-30 C) | 650 F (340 C) | 22 (6.7) | X | rubber | single upper | ||
LLDPE | 40 (1.0) | 65-85 F (18-30 C) | 750 F (400 C) | 20 (6.1) | X | steel | single/double | ||
LLDPE | 60 (1.5) | 65-85 F (18-30 C) | 800 F (425 C) | 18 (5.5) | X | steel | double/triple | ||
LLDPE | 80 (2.0) | 65-85 F (18-30 C) | 860 F (460 C) | 15 (4.6) | X | steel | double/triple | ||
Non-reinforced PVC/PP | 20 (0.5) | 65-85 F (18-30 C) | 650 F (340 C) | 25 (7.6) | X | X | rubber | single upper | |
Non-reinforced PVC/PP | 30 (0.75) | 65-85 F (18-30 C) | 700 F (370 C) | 22 (6.7) | X | X | rubber | single upper | |
Non-reinforced PVC/PP | 40 (1.0) | 65-85 F (18-30 C) | 750 F (400 C) | 20 (6.1) | X | X | rubber | single/double | |
Non-reinforced PVC/PP | 50-60 (1.27-1.5) | 65-85 F (18-30 C) | 800 F (425 C) | 18 (5.5) | X | X | steel | steel | double/triple |
Non-reinforced PVC/PP | 80 (2.0) | 65-85 F (18-30 C) | 860 F (460 C) | 15 (4.6) | X | X | steel | steel | double/triple |
Reinforced PP | 36 (0.9) | 65-85 F (18-30 C) | 750 F (400 C) | 32 (9.8) | X | steel | single/single | ||
Reinforced PP | 45 (1.1) | 65-85 F (18-30 C) | 750 F (400 C) | 32 (9.8) | X | steel | single/single | ||
Weight oz. / sq. yd. | |||||||||
Non-woven geotextile | 4 to 8 | 65-85 F (18-30 C) | 650 F (340 C) | 32 (9.8) | X | X | steel | steel | wedge disengaged |
Non-woven geotextile | 10 to 12 | 65-85 F (18-30 C) | 650 F (340 C) | 32 (9.8) | X | X | steel | steel | wedge disengaged |
Non-woven geotextile | 14 to 20 | 65-85 F (18-30 C) | 650 F (340 C) | 25 (7.6) | X | X | steel | steel | wedge disengaged |
Non-woven geotextile | 22 to 32 | 65-85 F (18-30 C) | 650 F (340 C) | 22 (6.7) | X | X | steel | steel | wedge disengaged |
Non-woven geotextile | Up to 50 | 65-85 F (18-30 C) | 650 F (340 C) | 18 (5.5) | X | X | steel | steel | wedge disengaged |
NOTE: The above parameters are intended as a basic starting point only and will need to be adjusted to compensate for each individual ambient and site condition. |
|||||||||
Manufacturer assumes no liability for weld quality using the above parameters!! |
Appendix B
Pro-Wedge Speed Setting versus Actual Travel Rate Chart
Speed setting versus actual travel speed (FEET PER MINUTE)
Setting | Low Gear | High Gear |
999 | 18 | 32 |
950 | 16 | 29 |
900 | 15 | 27.5 |
850 | 14 | 26 |
800 | 13 | 24.5 |
750 | 12.5 | 22.5 |
700 | 12 | 21 |
650 | 11 | 19.5 |
600 | 10 | 18 |
550 | 9.5 | 16.5 |
500 | 8.5 | 15 |
450 | 8 | 13.5 |
400 | 7 | 12 |
350 | 6 | 10.5 |
300 | 5.5 | 9 |
250 | 4.5 | 7.5 |
200 | 3 | 6 |
150 | 2 | 4 |
100 | 1 | 3 |
Setting | Low Gear | High Gear |
999 | 18 | 32 |
950 | 16 | 29 |
900 | 15 | 27.5 |
850 | 14 | 26 |
800 | 13 | 24.5 |
750 | 12.5 | 22.5 |
700 | 12 | 21 |
650 | 11 | 19.5 |
600 | 10 | 18 |
550 | 9.5 | 16.5 |
500 | 8.5 | 15 |
450 | 8 | 13.5 |
400 | 7 | 12 |
350 | 6 | 10.5 |
300 | 5.5 | 9 |
250 | 4.5 | 7.5 |
200 | 3 | 6 |
150 | 2 | 4 |
100 | 1 | 3 |
Setting | Low Gear | High Gear |
999 | 18 | 32 |
950 | 16 | 29 |
900 | 15 | 27.5 |
850 | 14 | 26 |
800 | 13 | 24.5 |
750 | 12.5 | 22.5 |
700 | 12 | 21 |
650 | 11 | 19.5 |
600 | 10 | 18 |
550 | 9.5 | 16.5 |
500 | 8.5 | 15 |
450 | 8 | 13.5 |
400 | 7 | 12 |
350 | 6 | 10.5 |
300 | 5.5 | 9 |
250 | 4.5 | 7.5 |
200 | 3 | 6 |
150 | 2 | 4 |
100 | 1 | 3 |
Speed setting versus actual travel speed (METERS PER MINUTE)
Setting | Low Gear | High Gear |
999 | 5.4 | 9.6 |
950 | 4.8 | 8.8 |
900 | 4.5 | 8.3 |
850 | 4.2 | 7.9 |
800 | 3.9 | 7.4 |
750 | 3.8 | 6.8 |
700 | 3.6 | 6.4 |
650 | 3.3 | 5.9 |
600 | 3 | 4.5 |
550 | 2.9 | 5 |
500 | 2.6 | 4.5 |
450 | 2.4 | 4 |
400 | 2.1 | 3.6 |
350 | 1.8 | 3.1 |
300 | 1.7 | 2.7 |
250 | 1.4 | 2.3 |
200 | 0.9 | 1.8 |
150 | 0.6 | 1.2 |
100 | 0.3 | 0.9 |
Setting | Low Gear | High Gear |
999 | 5.4 | 9.6 |
950 | 4.8 | 8.8 |
900 | 4.5 | 8.3 |
850 | 4.2 | 7.9 |
800 | 3.9 | 7.4 |
750 | 3.8 | 6.8 |
700 | 3.6 | 6.4 |
650 | 3.3 | 5.9 |
600 | 3 | 4.5 |
550 | 2.9 | 5 |
500 | 2.6 | 4.5 |
450 | 2.4 | 4 |
400 | 2.1 | 3.6 |
350 | 1.8 | 3.1 |
300 | 1.7 | 2.7 |
250 | 1.4 | 2.3 |
200 | 0.9 | 1.8 |
150 | 0.6 | 1.2 |
100 | 0.3 | 0.9 |
Setting | Low Gear | High Gear |
999 | 5.4 | 9.6 |
950 | 4.8 | 8.8 |
900 | 4.5 | 8.3 |
850 | 4.2 | 7.9 |
800 | 3.9 | 7.4 |
750 | 3.8 | 6.8 |
700 | 3.6 | 6.4 |
650 | 3.3 | 5.9 |
600 | 3 | 4.5 |
550 | 2.9 | 5 |
500 | 2.6 | 4.5 |
450 | 2.4 | 4 |
400 | 2.1 | 3.6 |
350 | 1.8 | 3.1 |
300 | 1.7 | 2.7 |
250 | 1.4 | 2.3 |
200 | 0.9 | 1.8 |
150 | 0.6 | 1.2 |
100 | 0.3 | 0.9 |
Appendix C
Warranty
DEMTECH Services, Inc. warrants all equipment of its manufacture to be free from defects in materials, workmanship, mechanical parts, and labor for a period of one year from the date of shipment to the original buyer and ninety days for electrical. This warranty excludes normal wear items such as gears, bearings and chains. The liability under this warranty is limited to replacement parts and labor on equipment when the equipment is returned prepaid to the factory or its authorized service center with prior authorization from DEMTECH Services, Inc., and upon examination by DEMTECH Services, Inc., is determined to be defective. At DEMTECH Services, Inc.’s option, a service representative may be dispatched to the equipment location.
As an additional protection, DEMTECH Services, Inc. warrants that for a period of 90 days from the date of shipment to the original buyer, pending prior authorization from DEMTECH Services, Inc., there will be no charge for service related shipping of parts and/or equipment or for authorized travel of a service representative to the equipment location. After 90 days, all costs incurred for shipping the equipment or parts thereof or for travel are the responsibility of the buyer. Our warranty for this equipment is rendered void if the unit has been repaired, taken apart or modified, or attempted to be, unless such actions have been taken in accordance with written instructions received from DEMTECH Services, Inc. The warranty is also void if the equipment has been subjected to abuse, accident or other abnormal conditions.
IF ANY FAULT DEVELOPS,
THE FOLLOWING STEPS SHOULD BE TAKEN:
- Notify DEMTECH Services, Inc. by calling 1-888-324-9353. Overseas customers should contact the local DEMTECH authorized service center. Please be prepared with the model number, serial number and full details of the difficulty. Upon receipt of this information, service data or shipping instructions will be provided by DEMTECH Services, Inc. Do not return the unit for repair without first contacting the factory or its representative for instructions.
- After the initial 90 day period, on receipt of shipping instructions, forward the equipment prepaid to the factory or its authorized service center as instructed. If requested, an estimate of the charges will be made before work begins, especially with those cases where the DEMTECH Services, Inc. product is not covered by the warranty.
- If the original carton and packing are not available, the product should be packed in a container with a strong exterior and surrounded by a protective layer of shock-absorbing material. DEMTECH Services, Inc. advises returning the equipment at full value to the carrier.
DEMTECH Services, Inc. reserves the right to make changes in design at any time without incurring any obligation to install the same changes on units previously purchased.
This warranty states the essence of the obligations or liabilities on the part of DEMTECH Services, Inc. THE FORMAL, COMPLETE AND EXCLUSIVE STATEMENT OF DEMTECH SERVICES, INC.’S WARRANTY IS CONTAINED IN ITS QUOTATIONS, ACKNOWLEDGEMENTS AND INVOICES. DEMTECH Services, Inc. neither assumes, nor authorizes any person to assume for it, any liability in connection with the sale of its equipment other than those set forth herein.